
Unmatched Placement Versatility and Speed with 3-Head Precision
The MC389 is engineered for unmatched flexibility, speed, and precision making it a standout solution for high-mix, mid- to high-volume production environments. Featuring a high-speed-3-head gantry, the MC389 achieves placement rates of up to 10,500 components per hour (CPH), maintaining accuracy without compromising throughput.
Standard capabilities include the placement of components as small as 01005 with a placement accuracy of 30 µm (3 Sigma), while also accommodating large and complex SMDs up to 100 x 150 mm. This extraordinary component range allows the MC389 to handle everything from ultra-miniature passives to oversized connectors and modules.
Precision alignment is driven by an advanced dual-vision system that pairs head-mounted Cognex® on-the-fly cameras with a stationary upward-looking camera. This combination enables highly accurate placement of challenging components such as BGAs, µBGAs, CSPs, MLFs, and fine-pitch QFPs down to 0.3 mm (0.012"). It also excels with odd-form components that require more than just body centering.
Unlike systems that rely solely on basic outline matching, the MC389 utilizes full-vision alignment to match leads, balls, or bumps directly to the pads on the PCB. This eliminates common placement inaccuracies and ensures consistent high-quality results, especially crucial when working with today's densely packed and miniaturized designs.
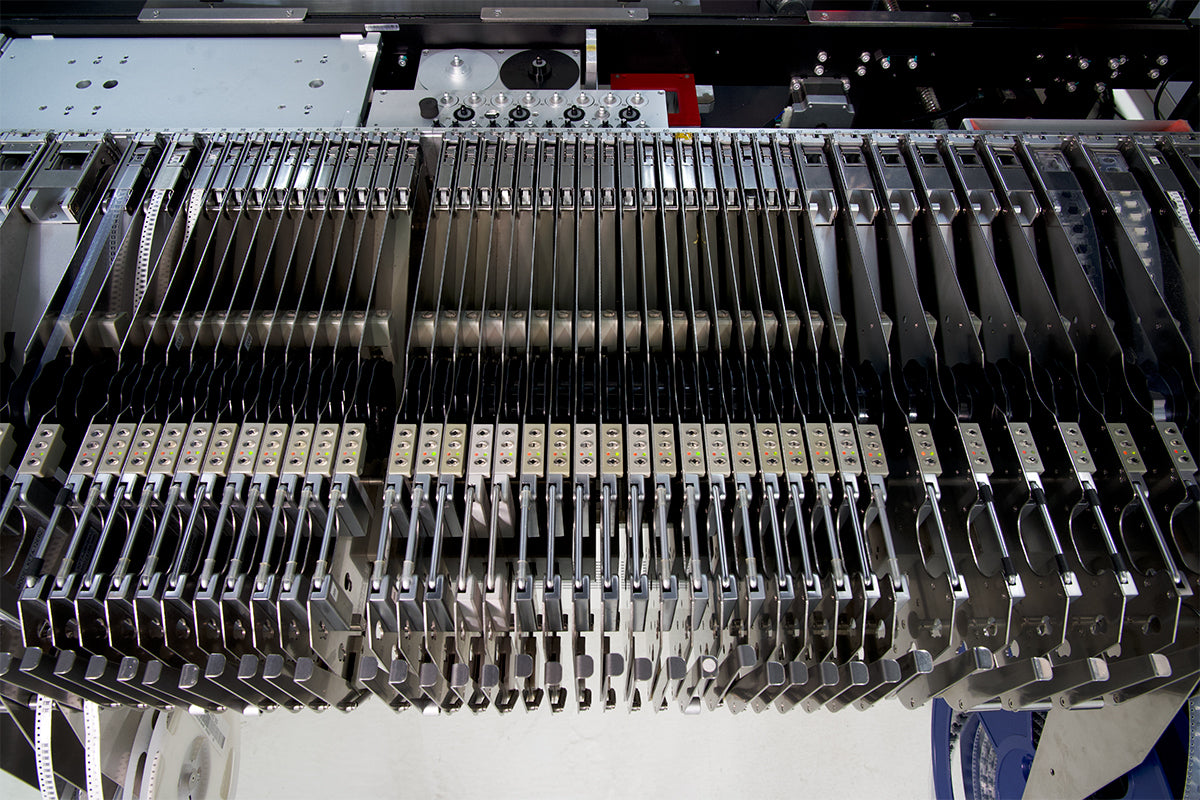
Flexible Feeder Capacity for High-Mix Efficiency
The MC389 offers exceptional flexibility and is most commonly configured with 96 feeder ports; this is ideal for high-mix, quick-turn production lines. In this popular setup, two 48-port feeder racks are mounted on the front and rear of the machine, enabling integration with an optional 3-stage SMEMA-compatible inline conveyor system. This configuration supports inline workflows and provides ample capacity for Smart tape feeders and stick feeders, making it well-suited for both mid- and high-volume production in automated environments.
For maximum feeder density, the MC389 can also be configured in a stand-alone or batch mode with a total of 160 feeder ports. This setup includes dual 48-port feeder racks at the front and rear, along with dual 32-port racks on each side. This expanded layout allows more components to remain resident on the machine, minimizing downtime during job changeovers and supporting a broader range of feeder types, including Smart Tape Feeders, stick feeders, waffle trays, and cut strip tape holders.
In either configuration, the MC389 features a large, open placement area of up to 650 mm x 460 mm (25.6" x 18.1"), depending on the number of feeder bases and the board handling method. The generous work surface accommodates flexible component presentation, including waffle trays and bulk or cut strip tape holders speeding up setup and changeover across a wide variety of board types and production needs. Whether operating in a work cell or inline environment, the MC389 delivers the capacity, adaptability, and efficiency modern SMT production demands.

Built for Speed, Precision, and Efficiency
Designed to meet the demands of high-volume SMT production, the MC389 simplifies complex processes to help you move faster and operate smarter. Its intelligent software automatically fine-tunes feeder placement, minimizing head movement and tool swaps to keep throughput high and downtime low.
Quick-change smart feeders—both tape and stick—connect effortlessly and are ready to run in moments. Electronic tape feeders deliver smooth, consistent indexing for repeatable accuracy, while fully adjustable stick feeders support a wide range of component sizes and packaging. Cut tape holders let you make the most of partial reels and smaller quantities, helping reduce waste and save on materials.
To speed up job prep and improve accuracy, the MC389 integrates with barcode scanners and supports offline feeder programming. That means less manual entry, fewer errors, and faster, more reliable job setup every time.

Consistency and Long-Term Dependability
Consistent results are non-negotiable, regardless of whether you're producing in-house or assembling boards for customers. The MC389 delivers with a rugged mechanical design and precision-engineered components that work together to maintain high accuracy and repeatability—even at full production speed.
At its core is a rigid, welded steel frame supporting a precision ball-screw system, advanced servo motors, and non-contact rotary encoders—all optimized for smooth, stable motion and reliable placement performance.
Your investment is protected with a standard 1-year warranty, plus built-in remote diagnostics for fast, expert support when you need it. With the MC389, you get more than just a machine—you get a performance-driven platform backed by responsive service and lasting peace of mind.

User-Friendly, Field-Tested Software Built for Efficiency
The MC389 runs on the same powerful, Windows®-based software platform used across the entire MC Series, refined over more than a decade through real-world customer feedback. The result is a system that is not only reliable and stable but also remarkably easy to use, even in demanding production environments.
Programming can be completed through CAD file import and conversion, manual teaching, or direct entry. After CAD import, users simply follow intuitive setup steps to configure the PCB layout, assign feeders, and define component placements making job setup fast and straightforward. Component data integrates seamlessly with the Smart Feeder system, streamlining both inventory control and production preparation. A built-in virtual PCB simulator visually displays the programmed assembly, allowing for quick verification of accuracy before production begins.
The production screen offers real-time monitoring of all pick camera images and provides clear visibility into production speed, current run time, task lists, and PCB status. The system tracks component placement in real time, enabling production to resume exactly where it left off in the event of an interruption. Operators can make on-the-fly adjustments to feeder settings, part placement, speed, or component data without ever leaving the production window, ensuring continuous workflow and maximum uptime.
Placement Specifications | |
---|---|
Number of Placement Heads | 3 |
Placement Rate (IPC-9850)* | 10,500 CPH |
Placement Accuracy | 30 µm, 3 Sigma |
Minimum Component Size | 01005 |
Maximum Component Size | 100 mm x 150 mm (3.94" x 5.9") |
Minimum Component Lead Pitch | 0.3 mm (0.012") |
BGA/CSP Placement Capability | Yes - Standard |
Alignment Method | Dual-Vision Alignment System |
Pick Up Specifications | |
Nozzle Changer | Included |
Number of Nozzles | 17 |
Accepts Additional Nozzles | Yes |
Integral Vacuum | Yes |
PCB Specifications | |
PCB Loading Method | Manual loading in batch / standalone configuration (standard) Single-stage and 3-stage inline conveyors (optional) |
Maximum Placement Area | 650 x 380 mm (25.6" x 15") with conveyor 650 x 460 mm (25.6" x 18.1") without conveyor |
Fiducial Recognition / Coordinate Correction | Yes |
Bad Mark Detection | Yes |
Feeder Capacity | |
Maximum Number of Feeder Ports | 96 with inline conveyor 160 batch configuration w/ feeders on four sides |
Maximum Number of Waffle Trays | Dependent on PCB size |
Programming | |
Operating System | Windows® Based |
PC, Keyboard, Mouse | Yes |
Monitor | Flat LCD |
Teaching Camera | Yes |
Numeric Data Entry | Yes |
CAD Download | Yes |
Step and Repeat for Matrix Boards | Yes |
Bar Code Reader for Feeders & Packaging | Yes |
MIS and Optimization Functions | Yes |
Off-Line Programming | Yes |
Dispenser Specifications | |
Dispensing Head | Optional |
Dispense Method | Time/Pressure |
Dot Size/Placement Speed | Down to 0.5 mm Up to 6,000 dots/hr |
Mechanical Specifications | |
X-Y Axis Drive Mechanism | Ball Screw |
X-Y Axis Drive Motors | AC Servo |
X-Y Axis Encoding | Rotary |
X-Y Axis Resolution | 0.005 mm (0.0002") |
Z Axis Drive Motor | DC Servo |
Z Axis Encoding | Rotary |
Z Axis Resolution | 0.02 mm (0.0008") |
θ Axis Drive Motor | DC Servo |
θ Axis Encoding | Rotary |
θ Axis Resolution | 0.045° |
θ Axis Range of Motion | 360° |
Physical Specifications | |
Overall Dimensions (Approx. L x W x H) | 1340 x 1478 x 1470 mm (52.7" x 58" x 57") |
Approx. Net Weight | 1100 kg (2425 lbs.) |
Facility Requirements | |
Standard Voltage | 200-230 VAC, 50/60 Hz |
Air Pressure | 80 psi, 9 CFM |
Service and Support | |
Remote Diagnostics | Included |
Warranty (Major Components) | 1 Year |

Smart Feeder Integration for Reliable Assembly
Every MC Series pick and place machine includes fully integrated smart feeder management and control software—built into the system from the ground up to enhance reliability, streamline efficiency, and ensure traceability throughout production. Each smart tape feeder features a DB-9 interface connector that plugs into any MC Series smart feeder base, enabling direct communication between the feeder and the machine’s software. A built-in memory module stores a unique feeder ID and essential component data, such as assigned port, feeder size and type, component value, lot and date codes, starting quantity, index increments, and package type.
To simplify job setup even further, an optional barcode reader can scan the part code on a reel and automatically upload all relevant information into the feeder. This eliminates manual data entry, reduces setup time, and prevents errors. Once connected, the system instantly applies the correct parameters, ensuring the right parts are always placed in the right positions. This seamless hardware-software integration allows MC Series machines to maintain consistently high assembly accuracy and efficiency, run after run.

New Innovative Feeder with Built-In OLED Display – KFTA3D Series
This next-generation smart feeder features an integrated OLED display and internal memory that continuously stores and updates key component information. Operators can instantly view reel quantities, feeder slot locations, part numbers, and part values whether the machine is running or offline. With real-time data visible directly on the feeder, setup becomes faster, more accurate, and less error prone. This added layer of visibility ensures the right components are loaded correctly from the start, preventing costly mistakes before they reach the inspection stage.
An internal battery ensures that stored data remains accessible even when the feeder is disconnected from the machine. Whether you’re tracking part usage during production or verifying setup offline, the system provides a consistent and reliable overview of component consumption. Additionally, these feeders are designed for efficient use of rack space; a 12 mm feeder only occupies a single slot, allowing for higher feeder density and greater flexibility during job setups. By shifting critical data access to the point of use, these smart feeders significantly improve both traceability and productivity in any high-mix SMT environment.

Universal Smart Stick Feeders for Maximum Flexibility
Manncorp’s smart stick feeders offer seamless integration with MC Series pick and place machines and can be positioned directly alongside smart tape feeders for efficient use of feeder rack space. Available in 5, 10, or 20-lane configurations, these feeders provide the flexibility needed for a wide range of component types and production requirements.
Using DB-9 interface connectors, each feeder communicates directly with the system software through the smart feeder base. Built-in memory modules store unique ID numbers that link each lane to its specific feeder position and associated data, including component specifications, belt indexing increments, and precise on/off timing for the vibratory mechanism. This intelligent design ensures accurate, consistent part delivery while simplifying setup and minimizing the risk of operator error.

Flexible Tray and Cut Tape Handling for MC Series Machines
MC Series pick and place machines feature spacious, open work areas designed to accommodate a variety of component presentation methods, including waffle trays and cut tape strips, for maximum flexibility during production.
The TS-1 Waffle Tray Holder occupies approximately 13” x 5.5” (330 mm x 140 mm) of the work area and is designed to securely hold a standard 12.4” x 5.35” (316 mm x 136 mm) JEDEC matrix tray—or up to two cut strip tape holders. Its adjustable design supports a wide range of smaller matrix tray and waffle pack combinations and can easily be modified for custom tray configurations as needed.
For low-quality components or those supplied in short tape lengths, CST Cut Strip Tape holders offer a practical solution. These holders allow operators to present components that are not long enough to be used with standard tape feeders, helping reduce waste and improve efficiency. Standard holders are available for 8 mm, 12 mm, 16 mm, and 24 mm tape widths, with additional sizes available upon request.

Smart Feeder Software: Seamless Setup, Tracking, and Changeover
Included as standard on all MC Series pick and place machines, Manncorp’s advanced smart feeder software simplifies and accelerates production with intelligent features that reduce setup time and eliminate manual data entry. From automatic quantity tracking to feeder position verification, the system ensures accurate, repeatable results across both short runs and high-volume jobs.
One of the key capabilities is automatic component quantity tracking. During production, the software continuously monitors component usage and updates each feeder’s onboard memory with the quantity remaining on the reel. This data is retained even after the feeder is removed. When reloaded—even for a different job—the feeder automatically communicates its remaining part count to the assembly program, allowing production to resume without recalibration or manual input.
Feeder position verification ensures components are being pulled from the correct locations. When optimized feeder positions are used, the machine compares smart feeder IDs with predefined slot data to confirm correct placement. If optimized positions are not used, the system can perform position scanning, identifying each feeder’s location automatically and mapping it to the corresponding pick-up point in the assembly file for fast, error-free changeovers.
To support flexible production environments, quick-change feeder location functionality allows operators to move feeders to new slots or maintain the same layout across consecutive runs without editing the pick and place program manually. For even greater convenience, an optional barcode reader can capture component data such as part value, lot code, date code, and starting quantity directly from packaging—cutting out time-consuming manual entry and reducing the risk of data entry errors.

Smart Tape Feeder Carts for Secure Storage and Off-Line Kitting
Safely transport, store, and organize your Smart Tape Feeders with Manncorp’s durable, dual-tiered Smart Tape Feeder Storage Cart. The FR-ST64 model (pictured) holds up to 64 individual 8 mm Smart Tape Feeders, making it ideal for off-line kitting and streamlined production preparation. Designed for mobility, the cart moves easily from the kitting area to the production line, helping operators stage feeders in advance for faster setup and changeover.
Built with heavy-duty tubular steel construction, the cart holds each feeder securely in place while protecting against bumps and impact during transport. Whether you’re preparing for a high-mix production run or simply looking to keep your feeders organized and damage-free, the FR-ST64 is a reliable, space-saving solution for any SMT operation.

Automatic Index Adjustment to Eliminate Pickup Errors
MC Series pick and place machines feature automatic index adjustment using vision-board alignment. When a new reel is loaded into a feeder, the machine can detect slight offsets in tape pocket position and automatically advance or reverse the feeder to correct it—ensuring accurate component pickup from the start. This is especially valuable when switching reels, as minor misalignments between tapes can lead to placement errors. For reels with looser tolerances, the system can be set to verify alignment and adjust indexing on every pickup, preventing recurring errors and maintaining consistent, reliable performance.
Inline options with conveyor and w/o waffle trays

Inline options with conveyor and with waffle trays

Batch Configurations w/o conveyor and w/o waffle trays

Batch Configurations w/o conveyor and with waffle trays
